How to Start a Manufacturing Business: A Step-by-Step Guide
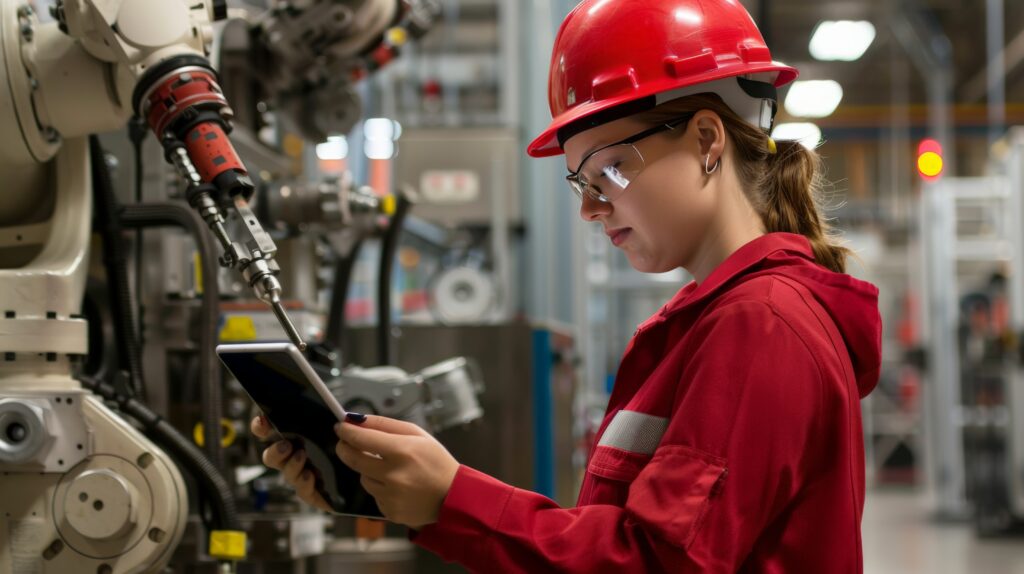
how to start a manufacturing business
Starting a manufacturing business can be a rewarding venture, enabling you to create high-demand products and tap into various markets. However, it also requires significant planning, resources, and industry knowledge. Here’s a comprehensive guide on how to start a manufacturing business.
1. Conduct Market Research and Choose Your Niche
- Identify Market Demand: Look into current trends and demands within different industries to see where your manufacturing business could fit best.
- Choose a Product or Market Segment: Focus on a specific type of product (e.g., eco-friendly packaging, custom electronics, or clothing) to build expertise and cater to a targeted customer base.
- Competitive Analysis: Research your competitors’ products, pricing, and market reach. Look for areas where you can improve or differentiate.
2. Create a Business Plan
- Define Business Objectives: Outline your goals and vision for the business, including growth targets, areas of specialization, and customer segments.
- Budgeting and Financial Forecasting: Develop an initial budget that accounts for equipment, raw materials, labor, facilities, and other operating costs. Project revenues and expenses for the first few years.
- Choose a Business Structure: Decide on a structure (LLC, corporation, etc.) that suits your business needs, providing legal and financial protections.
3. Secure Funding
- Explore Funding Options: Manufacturing requires significant capital, so explore funding through business loans, grants, investors, or even crowdfunding.
- Build a Compelling Pitch: Prepare a strong business case if you need to approach investors. Highlight your product’s potential, market demand, and operational plans.
4. Set Up Your Manufacturing Facility
- Location and Space Requirements: Choose a location that’s convenient for supply chain management and shipping to your target markets.
- Procure Necessary Equipment: Invest in reliable machinery, tools, and technology needed for production. Consider buying used or leasing equipment initially to reduce costs.
- Safety and Compliance: Ensure your facility meets all local safety and environmental regulations. Install safety equipment, conduct regular training, and adhere to industry best practices.
5. Build Your Supply Chain
- Identify Reliable Suppliers: Establish relationships with suppliers for raw materials. Having multiple suppliers can protect against shortages.
- Inventory Management: Decide on inventory levels and storage requirements. Efficient management of materials and finished goods reduces waste and saves money.
- Logistics and Shipping: Set up a dependable logistics plan for receiving materials and delivering finished products to customers.
6. Develop Your Production Process
- Design Workflow: Create a production process that maximizes efficiency, minimizes waste, and ensures quality. Lean manufacturing techniques can help reduce costs and increase productivity.
- Establish Quality Control: Implement quality assurance checks throughout the production cycle to catch issues early and maintain consistency.
- Hire Skilled Workers: A skilled team is essential for manufacturing. Look for workers with relevant experience and offer training programs to ensure efficiency.
7. Create a Marketing and Sales Strategy
- Build Brand Awareness: Develop a strong brand identity, including a logo, website, and social media presence to reach your target audience.
- Engage in B2B Sales: For many manufacturing businesses, direct-to-business sales and partnerships will be key. Attend industry events and trade shows to meet potential clients.
- Offer Sample Products or Trials: If possible, offer samples or trial orders to establish trust and demonstrate product quality.
8. Implement Technology for Better Management
- Manufacturing Software: Invest in software to help manage inventory, scheduling, and production processes.
- Customer Relationship Management (CRM): A CRM system can help you manage client interactions, follow-ups, and sales tracking.
- Data Analytics: Use data to monitor production costs, quality control issues, and customer feedback, adjusting operations as needed.
9. Stay Compliant and Continuously Improve
- Regulatory Compliance: Stay updated on industry-specific regulations for product safety, environmental impact, and labor laws.
- Review and Improve Processes: Regularly review production processes for efficiency, cost-saving opportunities, and improved quality.
- Customer Feedback: Listening to your customers can provide insights to help you improve your products and adapt to market demands.
Final Thoughts
Starting a manufacturing business requires dedication, attention to detail, and a clear strategy. By following these steps, you can establish a strong foundation, attract customers, and grow a successful manufacturing operation. As your business grows, stay adaptable, look for new opportunities, and continuously optimize your processes for sustainable success.